5 Misconceptions About Manufacturing Quality
High QA
June 25, 2021
Quality matters. It is important in any manufacturing facility but most critical for certain types of manufacturers in aerospace, automotive and medical industries and in high-precision part suppliers. Failure to maintain quality could result in injury or death. And none of us want that.
So why then, is quality a top priority until it requires an investment or needs to be implemented?
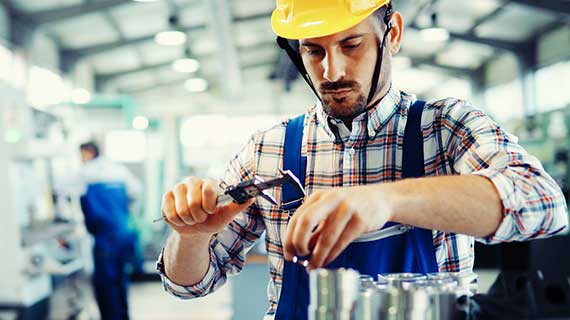
There are several misconceptions or myths among most manufacturing companies that keep them from implementing quality procedures. But these 5 myths – a synonym for excuses – are most common.
#1 - Quality Is a Final Destination
Quality is often seen as something done at the end of the manufacturing process. Manufacturers inspect for defects at the end of a production cycle and when problems are spotted, corrections are made after the fact. This causes a huge amount of waste, increases production times, and passes on higher costs to the end consumer. Rather than wait until an entire batch is produced with flaws, manufacturers should take advantage of the technology that enables them to identify and correct problem areas before a final product is completed. Implementing a QMS system with in-process checks can identify and correct problem areas before an entire manufacturing line is shutdown thus helping to reduce downtime and costs.
#2 - Quality Is Not My Responsibility
Unfortunately, quality groups in a company are often thought of as “that group over there” or “the ones that find problems.” Quality should be considered a vital part of every person in manufacturing. It is a company mindset and not just a destination. When a factory manager places a high regard on quality, employees will rise to meet the expectations. Employees sense the commitment in their management and feel that what they do is important. With a rise in a commitment to quality, production processes improve, non-conformances drop and scrap is minimized. When managers and employees are involved in preventative and corrective processes, quality improves, customer complaints are reduced, and businesses succeed.
#3 - Quality Is Expensive
While there are upfront costs of implementing a quality management system, it should be considered an investment. When quality is standardized and incorporated into all processes, both risks and costs are reduced. Manufacturing processes are streamlined, interpretation errors are prevented, quality control bottlenecks are identified and corrected which makes your company more efficient, productive and successful.
#4 - Quality Is Filled with Documentation and Paperwork
Quality documentation is unavoidable for manufacturing. In spite of time-consuming processes and frustrations it may cause, if you want to do business you must supply documentation. Those frustrations are only increasing with customers requiring more documentation and expecting to receive it faster. Too often manufacturing facilities are stuck with old manual paper processes and massive amounts of Excel spreadsheets. Investing in a manufacturing quality management system (QMS) will help alleviate some of the frustrations. Documentation is digitally stored, accessible when needed and there is only one source of truth. Digital quality documentation workflows are much more efficient than the manual alternative.
#5 - Quality Is Only for Big Companies
If you manufacture products, then you need a quality management system. It will help you keep track of documentation, quality records, forms and client and regulatory requirements. But more than that, a manufacturing QMS helps identify manufacturing bottlenecks, monitors production and records KPIs to ensure an efficient production process. With data stored in one location, managers can edit and make changes to the documents in real-time and get digital approval in minutes. Audits are simplified and traceability and accountability are detailed. Implementing a QMS solution ensures that your company follows GMP (good manufacturing practice) and complies with your industry standards and regulations.
Quality isn’t just a process or an activity — it’s a strategy and culture. While it may take effort to implement a manufacturing QMS solution, the benefits in the end will be immense for your business. The market is always in need of quality products, and if you deliver, you will stay in business for decades to come.
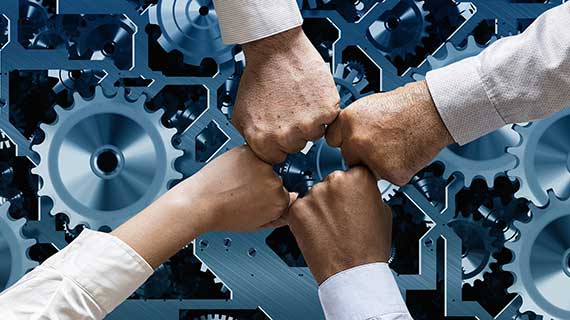
Learn more about improving manufacturing quality to ensure your customers are always confident in the products you manufacture. For more information, visit www.HighQA.com or contact a High QA representative for a free no-obligation demo of Inspection Manager, the ultimate manufacturing quality management software.