As you are probably aware by now, Ford Motor Company released their Customer-Specific Requirements for the IATF 16949 standard in January of 2022. The first question many people have is, “If we have a standard for companies to follow, why are there customer-specific requirements on top of the standard? Doesn’t that negate the need for a standard in the first place?” It’s a very valid point and one that’s under continual scrutiny.
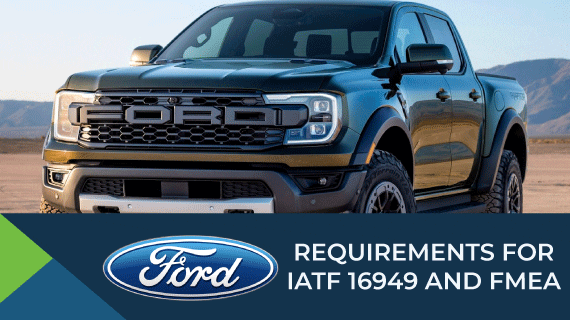
However, instead of focusing on the debate on whether there should or should not be additions to a standard, let’s focus on just what some of those changes are – namely the PFMEA requirements.
As anyone who has been in quality more than 13.2 seconds knows, Microsoft Excel is your friend. It’s literally used in place of documents, links, pictures, calculators, and databases. It’s a complete 1-stop-shop for all things in manufacturing requiring data, forms, and some semblance of interconnectedness between them. However, the one huge black eye it does get, is its lack of interconnectedness between it and other systems (without extensive back-end work).
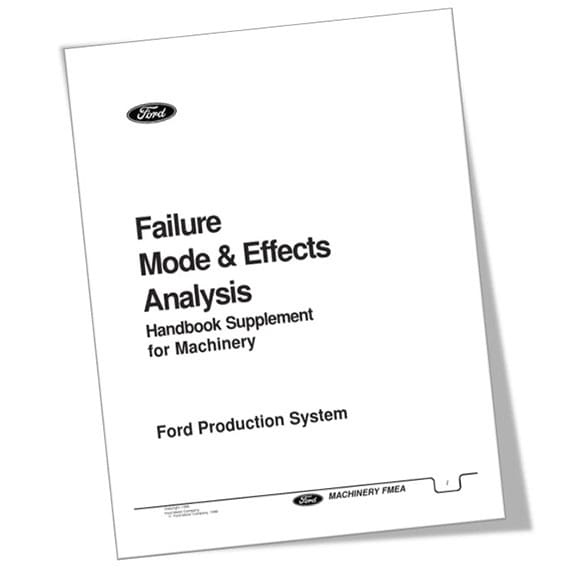
That brings us to the Ford PFMEA requirements. What is a PFMEA? Briefly, PFMEA stands for Process Failure Mode and Effects Analysis. It is a systematic and proactive approach used in various industries to identify potential failure modes in a process and assess their potential effects. The main purpose of PFMEA is to prevent or mitigate potential problems before they occur, thus improving the overall quality and reliability of the process or product.
The PFMEA process involves a team analyzing each step of a process to identify failure modes – ways in which the process could potentially fail to produce an acceptable part. For each failure mode, the team then assesses its severity (impact on the process), occurrence (likelihood of the failure mode occurring), and detection (likelihood of the failure mode being detected). The outcome of a PFMEA is a prioritized list of potential failure modes, ranked by their Risk Priority Number (RPN), which is calculated by multiplying the severity, occurrence, and detection ratings. This rating allows the team to focus on high-risk areas and develop appropriate actions or controls to prevent the identified potential failures.
From a documentation standpoint, a common practice with a PFMEA is to take the documentation of a part that is similar to the part you are compiling the submission package for and ‘copy and paste’ it over to the new submission package and change the necessary information (failure modes, occurrences, etc.) that are relevant for the new part. This is an inherently error-prone process with items missed or omitted and not entirely reviewed properly or comprehensively. Therefore, when the final PPAP submission package is created, the PFMEA being a vital component of the PPAP, it is rejected, and the supplier has to fix and resubmit.
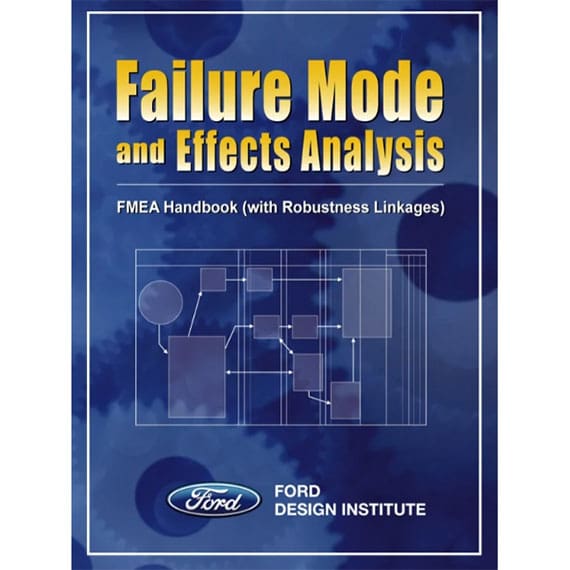
This is the issue that Ford is correctly trying to prevent.
The new Ford PFMEA standard requires the information associated with the Processes identified on the PFMEA to be generated from a controlled repository of data – ideally, but not specifically, from a database. An Excel-generated PFMEA will not be allowed or approved by FoMoCo.
The High QA PQP module takes this challenge head-on and conforms to the new Ford-specific requirements on top of the IATF 16949 standard by utilizing a database-driven Process Library within the Inspection Manager application. This Process Library contains all necessary “master” information for the Processes at your facility, including Severity, Occurrence, and Detection information and auto-calculated RPN values. This “master” information is used to auto-generate the PFMEA document within High QA.
What does the PFMEA generation process look like? Simply this:
- Balloon the print (High QA automates this too!)
- Identify the characteristics linked to each manufacturing operation
- Link the Process to the Operation (simple pull-down menu)
- Generate the PFMEA
PFMEA Generation will become an automated, consistent, and controlled process that can be done in a few minutes instead of the manual, error-prone Excel method of old.
Contact High QA or visit us at major industry events to find out more about PPAP submission generation using High QA PQP!
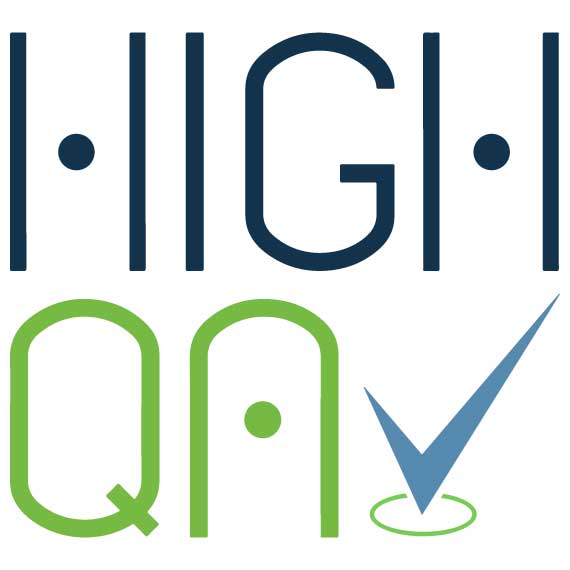
For more information, visit www.HighQA.com or contact a High QA representative for a no-obligation demo of High QA software, the ultimate manufacturing quality management software.